Table of Contents
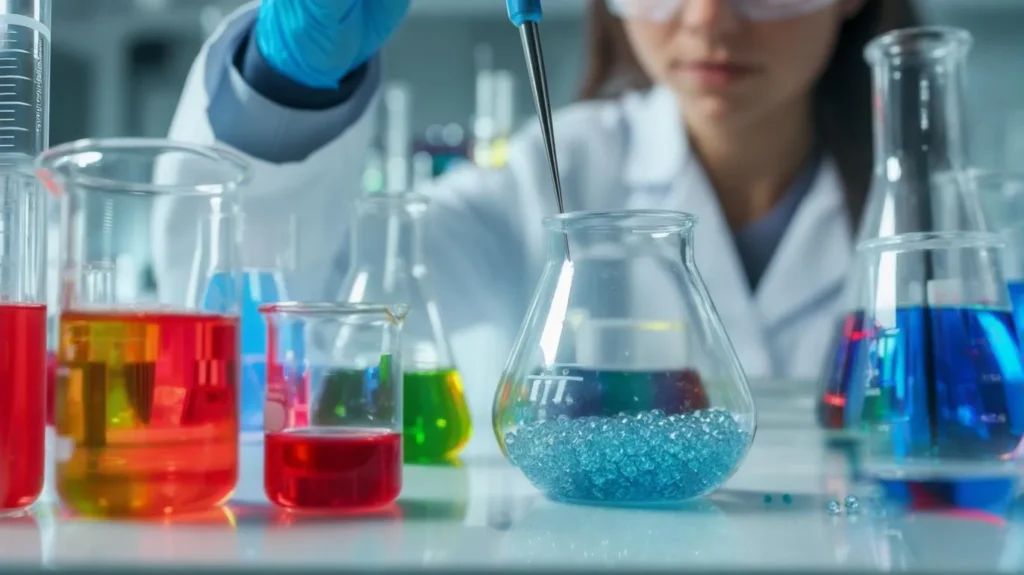
Plastic is an integral part of our daily lives, present in everything from packaging and containers to toys, electronics, and automotive parts. It has revolutionized industries and reshaped consumer habits due to its versatility, durability, and low cost. However, many people remain unaware of how plastic is made and what materials are involved in its production. In this article, we will explore the essential question: what is plastic made from? We will delve into the chemical processes, raw materials, and environmental implications associated with plastic production.
The Basics of Plastic
Plastic is a synthetic material derived from polymers—large molecules made up of repeating units called monomers. The term “plastic” encompasses a wide range of materials, including polyethylene (PE), polypropylene (PP), polyvinyl chloride (PVC), polystyrene (PS), and polyethylene terephthalate (PET), each varying in properties and applications. The journey from raw materials to finished products involves complex processes that transform these basic components into the familiar items we use every day.
Raw Materials Used in Plastic Production
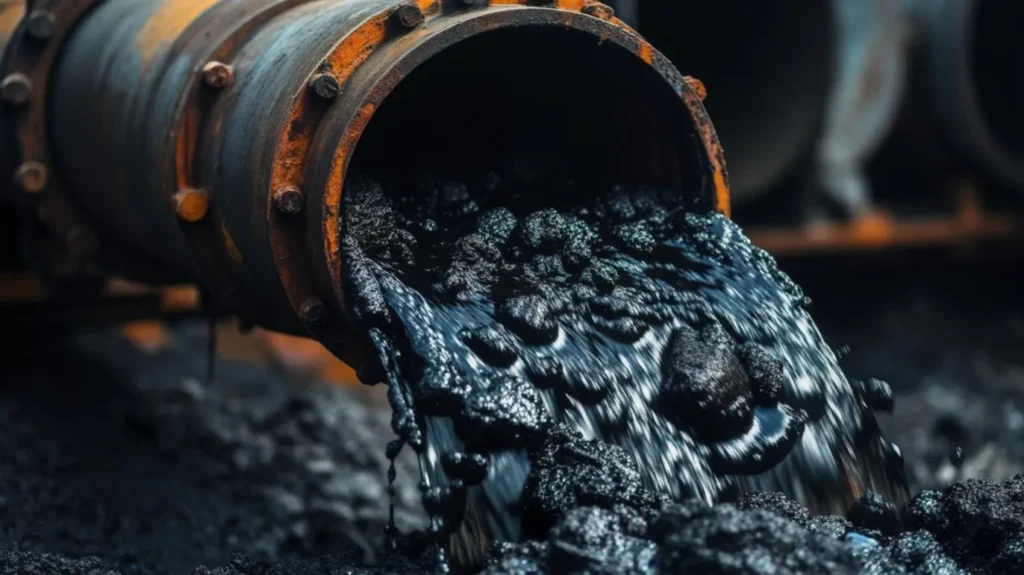
The primary raw materials for producing plastic are derived from fossil fuels, although bio-based alternatives are emerging. Here, we explore the traditional materials that make up most of the world’s plastic production.
1. Hydrocarbons
The most common source of plastic is hydrocarbons, primarily derived from petroleum (crude oil) or natural gas. The extraction and refining of these fossil fuels yield a variety of compounds used as feedstocks for plastic production.
- Crude Oil: Crude oil undergoes a refining process called fractional distillation, separating it into different components based on their boiling points. The lighter fractions, primarily alkanes, are crucial for producing base chemicals used in the creation of plastics.
- Natural Gas: Natural gas, primarily composed of methane, is another significant source for plastic synthesis. It can be processed into ethylene and propylene, key building blocks for plastics.
2. Ethylene and Propylene
Ethylene and propylene are the two primary raw materials used in the synthesis of many plastics.
- Ethylene: This colorless gas is produced through the cracking of hydrocarbons and is a foundational building block for polyethylene (PE) and polystyrene (PS). Ethylene polymerization generates several plastic forms, including low-density polyethylene (LDPE) and high-density polyethylene (HDPE).
- Propylene: Similarly produced from oil and gas, propylene is the key monomer for polypropylenes (PP). This versatile plastic is utilized in various applications, from packaging materials to automotive components.
3. Vinyl Chloride
Polyvinyl chloride (PVC) is one of the world’s most used plastics, and its production starts with vinyl chloride, a toxic gas. Vinyl chloride is synthesized via the reaction of ethylene and chlorine, typically derived from salt. The polymerization of vinyl chloride yields flexible or rigid PVC, depending on processing techniques and additives.
4. Terephthalic Acid and Ethylene Glycol
Polyethylene terephthalate (PET) is a widely used plastic, especially in the beverage industry for bottles. Its production involves two key components: terephthalic acid and ethylene glycol. Terephthalic acid is produced through the oxidation of para-xylene, while ethylene glycol is derived from ethylene. The polyesterification of these two components results in PET, a lightweight and strong plastic often favored for its recyclability.
5. Other Additives
To enhance specific properties and characteristics of plastics, various additives are introduced during the production process. These can include:
- Stabilizers: Added to protect plastics from degradation due to heat and UV exposure.
- Plasticizers: Used to increase flexibility and workability, particularly in PVC products.
- Colorants: To give plastics their desired colors and aesthetic appeal.
- Fillers: Such as calcium carbonate or talc, which can improve mechanical properties and reduce manufacturing costs.
The Plastic Manufacturing Process
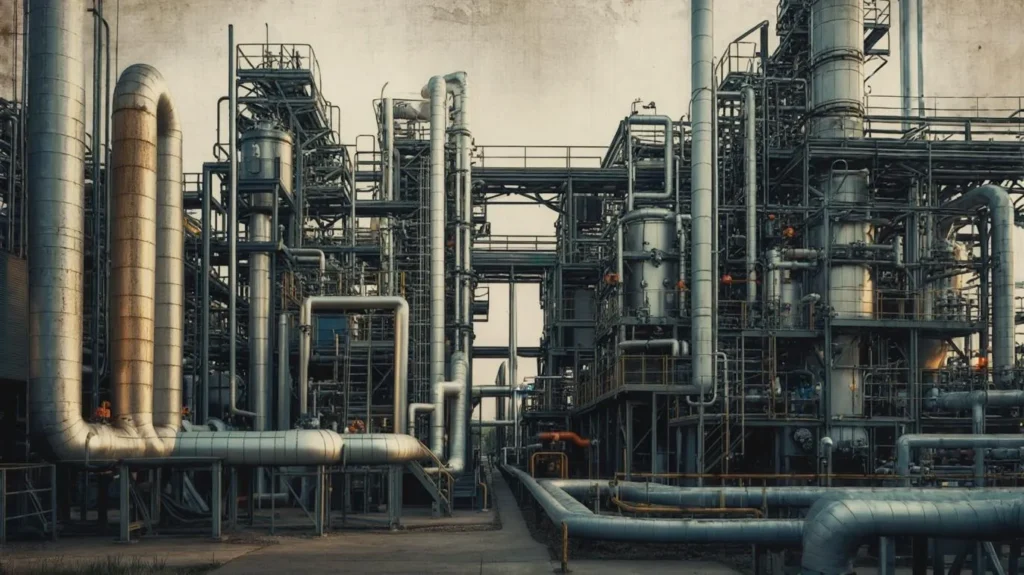
Once the raw materials have been synthesized, the manufacturing process begins. Here are the common steps involved in turning these raw inputs into finished plastic products:
1. Polymerization
The first step in manufacturing plastic is polymerization, a chemical reaction in which monomers join to form a polymer chain. This process can occur through various methods, including:
- Addition Polymerization: In processes like ethylene polymerization, monomers add together without producing by-products, resulting in chain growth.
- Condensation Polymerization: Involves the loss of a small molecule, usually water, during the reaction. This method is often used for producing polyesters like PET.
2. Compounding
Once the polymer is created, it is often compounded with various additives to enhance its properties. Compounding involves mixing the polymer with stabilizers, plasticizers, colorants, and fillers to achieve the desired characteristics forspecific applications. This process is typically performed in an extruder, where heat and mechanical energy facilitate the uniform distribution of additives throughout the polymer matrix.
3. Shaping and Forming
After compounding, the plastic is shaped into its final form through several methods. The choice of shaping technique depends on the type of plastic, the intended application, and the desired final product. Common shaping methods include:
- Injection Molding: This technique involves injecting molten plastic into a mold, where it cools and solidifies into the desired form. Injection molding is widely used for producing complex and detailed parts, such as bottle caps, toys, and automotive components.
- Blow Molding: Primarily used for making hollow objects, such as bottles and containers. In this process, air is blown into a heated plastic tube, expanding it to fit the shape of a mold.
- Extrusion: In this continuous process, plastic is melted and forced through a die to create long shapes like pipes, sheets, or films. Extruded products can be cut to size for various applications.
- Thermoforming: This method involves heating a plastic sheet until pliable and then forming it over a mold. It is commonly used for making packaging materials, trays, and clamshell containers.
4. Finishing
Once molded or shaped, plastics often undergo finishing processes, which may include trimming, coating, printing, or assembly. Finishing ensures that the final product meets the required aesthetic and functional standards for its intended use.
Environmental Considerations in Plastic Production
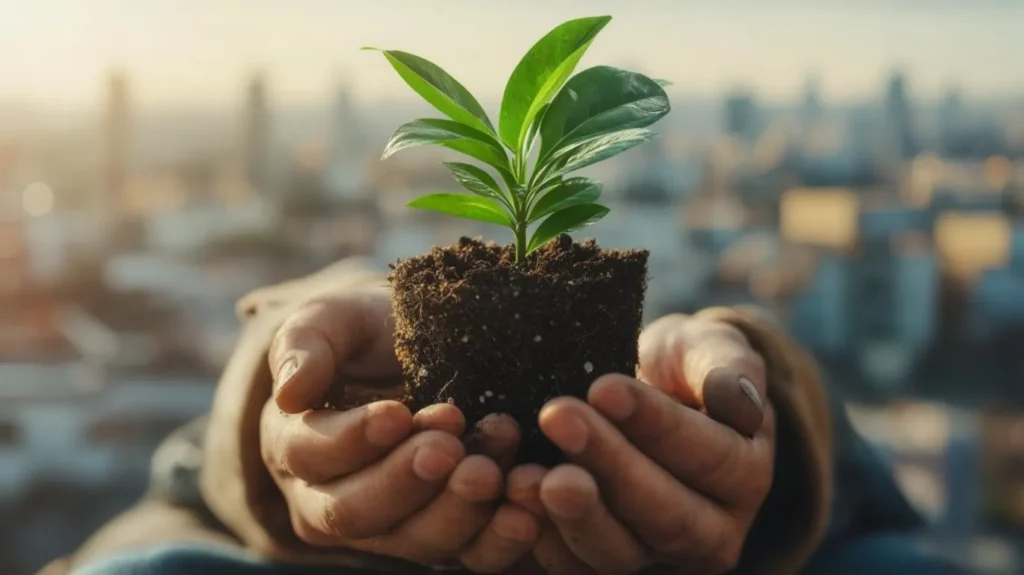
While the versatility and utility of plastic are undeniable, the environmental implications of its production and use cannot be overlooked. As society grapples with plastic pollution, it’s essential to address the following challenges:
1. Resource Consumption
The extraction and processing of fossil fuels not only contribute to the depletion of natural resources, but they also release significant greenhouse gases into the atmosphere. As the demand for plastics continues to grow, finding sustainable alternatives and reducing dependence on fossil fuels becomes increasingly important.
2. Waste Management
Plastic waste is a global crisis, with millions of tons ending up in landfills and oceans every year. The durability and resistance to degradation that make plastic appealing also result in long-term environmental consequences. The accumulation of plastic waste harms wildlife, pollutes ecosystems, and poses risks to human health.
3. Recycling Challenges
Although recycling can mitigate some of the environmental impacts of plastic, the current rates of plastic recycling are alarmingly low. Contamination, lack of proper infrastructure, and limited market demand for recycled materials hinder effective recycling efforts. Additionally, the chemical composition of different plastics complicates the recycling process as various types must be sorted and processed separately.
4. Innovations in Bioplastics
In response to the growing concerns surrounding plastic waste, many researchers and companies are exploring alternatives, such as bioplastics. These materials are derived from renewable biological sources such as corn starch, potato starch, or sugarcane, offering a more sustainable option compared to traditional fossil fuel-based plastics. Bioplastics can be designed to be biodegradable, reducing their impact on the environment.
Conclusion: What Is Plastic Made From and the Future Ahead
In summary, understanding what plastic is made from involves looking at the complex interplay of raw materials, polymerization processes, and production techniques. Plastics are primarily derived from hydrocarbons sourced from fossil fuels, with significant contributions from coal and natural gas, highlighting the ongoing reliance on non-renewable resources.
While the traditional plastic production process has revolutionized industries and consumer products, the environmental implications of plastic waste present a pressing challenge for our planet. The conversation surrounding plastic must shift toward promoting sustainable materials, enhancing recycling efforts, and minimizing single-use plastics through public awareness and legislative action.
As society pushes for change, the future of plastic holds promise due to advancements in bioplastics, improved recycling technologies, and innovative design practices that prioritize sustainability. By understanding the origins and composition of plastic, we can make informed choices, drive change toward a circular economy, and work collectively to minimize our environmental footprint. Ultimately, the ongoing question of what plastic is made from opens the door to broader discussions about responsible consumption and the development of sustainable materials that can safeguard the planet for future generations.