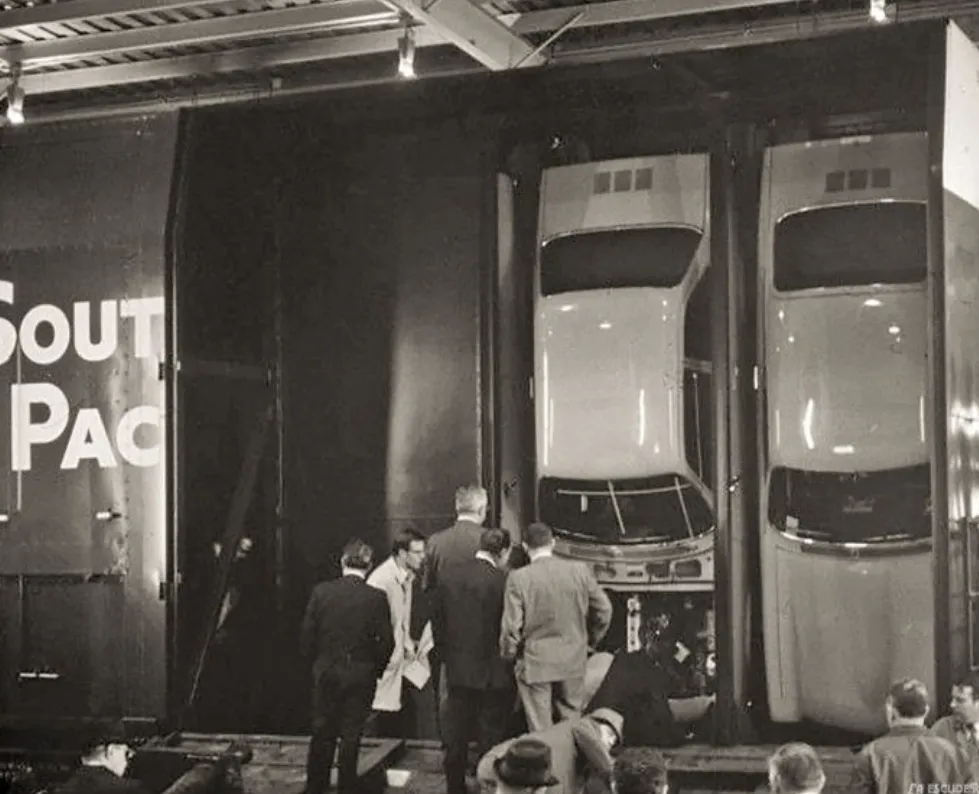
Engineering Beyond the Assembly Line
In the automotive world, innovation often drives attention toward performance, aesthetics, or manufacturing processes. Yet one of the most unique and ambitious innovations of the 1970s had little to do with what happened on the road or the factory floor. It was about what happened between the factory and the showroom: logistics. “The Chevrolet Vega being loaded vertically” isn’t just a quirky historical anecdote it’s a profound example of how creative problem-solving reshaped an entire segment of automotive transport.
This article delves deep into the remarkable logistical innovation that allowed the Chevrolet Vega to be shipped in an upright position using the Vert-A-Pac system. From engineering modifications to railroad collaboration, and economic implications to legacy, this is the comprehensive story of how a compact car turned rail transport on its head literally.
The Need for a Smarter Shipping Strategy
In the late 1960s, General Motors (GM) anticipated an explosion in demand for compact, fuel-efficient vehicles. The Chevrolet Vega, launched in 1970, was designed to compete directly with foreign imports. However, GM faced a significant hurdle: efficiently transporting tens of thousands of these new vehicles across the country.
Standard tri-level railcars could carry 18 vehicles, a capacity inadequate for GM’s volume requirements. The solution needed to be not only more space-efficient but also cost-effective and safe. Thus emerged a groundbreaking collaboration with Southern Pacific Railroad, culminating in the Vert-A-Pac railcar system a marvel of industrial ingenuity.
The Vert-A-Pac System: Turning Cars on Their Nose
The concept behind the Vert-A-Pac was daring: why not load cars vertically, nose-down, to maximize the use of available space within a railcar? This idea evolved into a design that allowed each specialized railcar to carry up to 30 Chevrolet Vegas an impressive 67% increase over traditional methods.
The railcars featured vertical slots into which the Vegas were mounted using special cast-steel sockets attached to the undercarriage. These sockets provided rigid support, preventing movement or structural damage during transit. The railcar doors doubled as load-bearing platforms and secured the vehicles in place.
This novel approach wasn’t just about stacking more cars; it was a comprehensive rethinking of vehicle transport logistics.
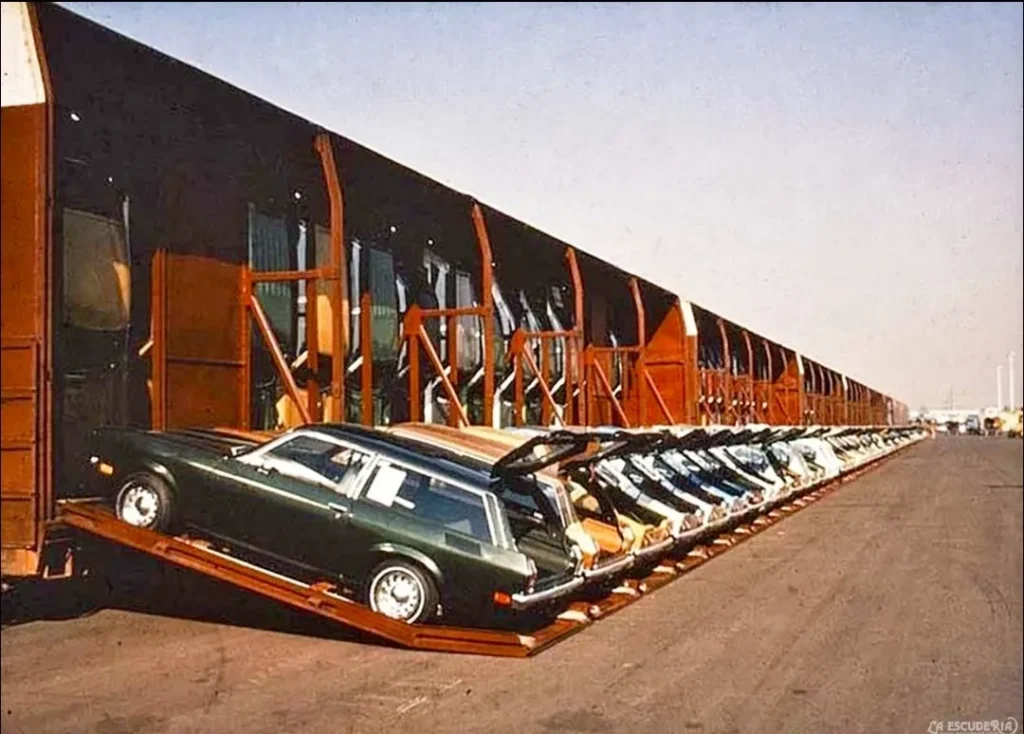
Engineering Modifications for Vertical Shipping
To accommodate the unconventional orientation, GM engineers had to rethink several aspects of the Chevrolet Vega’s design. The modifications ensured that critical fluids and components would remain stable and safe during vertical transport:
- Engine Baffling: Baffles were added inside the engine to prevent oil from flooding the number one cylinder while the car was nose-down.
- Fuel Management: The carburetor was fitted with a specialized drain tube to redirect gasoline into a sealed vapor canister, preventing leakage and vapor buildup.
- Washer Fluid Positioning: The windshield washer reservoir was tilted at a 45-degree angle, ensuring it would not spill or create pressure imbalances.
- Battery Engineering: The Vega’s battery had filler caps positioned high on the rear edge to prevent acid spillage during transit.
- Suspension and Powertrain Support: Plastic spacers were inserted beside the engine and transmission to prevent strain on mounts. These were removed at the destination.
Each modification was reversible or designed to blend seamlessly into the car’s standard configuration, ensuring minimal impact on the end-user experience.
Safety Measures and Handling Protocols
While the Vert-A-Pac system was an engineering marvel, safety remained paramount. GM and Southern Pacific Railroad implemented strict handling protocols to ensure that the vertically loaded vehicles arrived at dealerships undamaged:
- Soft-Touch Locking Mechanisms: The railcars used precision locking clamps and shock absorbers to secure the vehicles without damaging the exterior.
- Unloading Procedures: Special unloading stations were built at distribution hubs. Workers used hydraulic systems to gently lower and extract each Vega.
- Training for Personnel: Both railroad and GM employees underwent training to properly manage the loading and unloading process, minimizing human error and mechanical strain.
This approach reinforced GM’s commitment to delivering quality even before the car reached the dealership lot.
Economic and Environmental Impacts
The primary goal of the Vert-A-Pac system was to reduce transportation costs and it succeeded. By increasing vehicle density per railcar by nearly 70%, GM significantly lowered the per-unit shipping cost of each Vega. This reduction helped the company offer the Vega at a competitive price point, making it more appealing to budget-conscious American consumers.
Moreover, this efficient use of railcar space also contributed to a reduced environmental footprint. Fewer railcars were needed to move the same number of vehicles, reducing fuel consumption and associated emissions. Although the term “green logistics” wasn’t in vogue in the 1970s, the Vert-A-Pac system was a pioneering example.
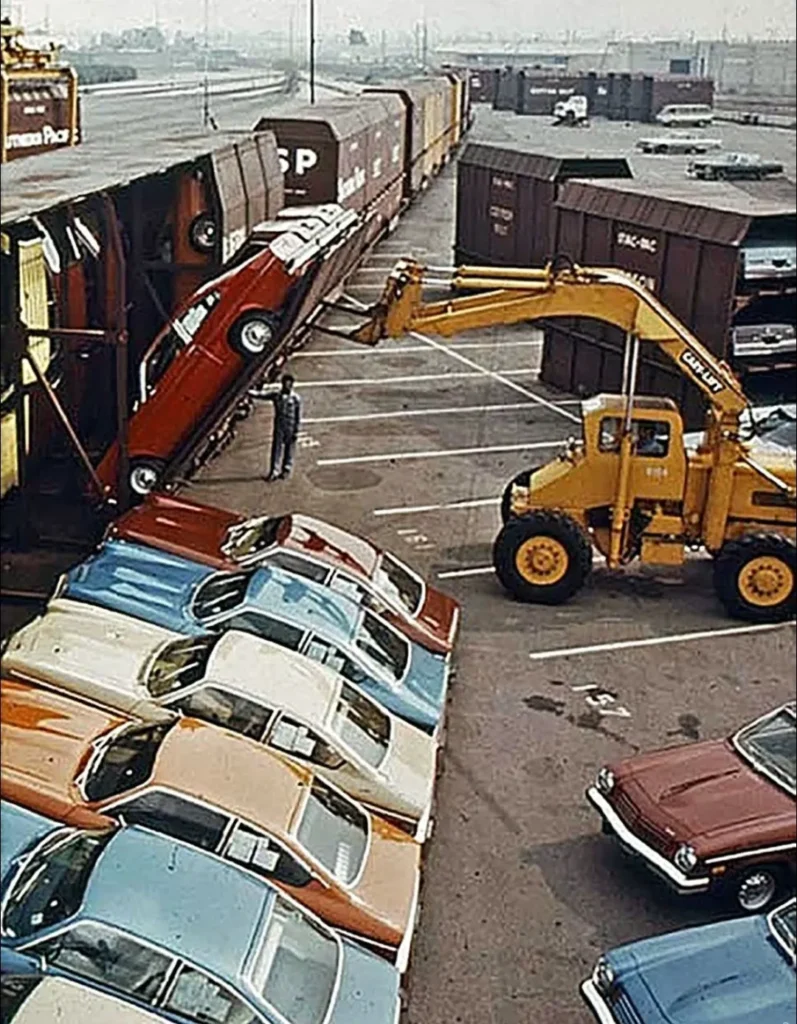
Public Perception and Marketing Angle
Although the public didn’t often see the vertical loading process firsthand, GM leveraged the uniqueness of the Vert-A-Pac system in its marketing campaigns. The idea that the Vega was designed with such forward-thinking logistics in mind added to its futuristic appeal.
Advertisements and trade publications highlighted the engineering prowess behind the car and its transportation. It became a talking point that helped set the Vega apart in a crowded marketplace even if the logistics marvel was largely invisible to the average consumer.
Challenges and Drawbacks
Despite its ingenuity, the Vert-A-Pac system wasn’t without its challenges:
- Specialized Infrastructure: Only specific rail routes and unloading facilities could accommodate the Vert-A-Pac cars, limiting flexibility.
- Vehicle Design Constraints: The modifications required for vertical shipping added complexity to the manufacturing process.
- Post-Shipment Prep: Dealerships had to remove certain protective elements and inspect the vehicle more thoroughly upon arrival.
As a result, the system remained exclusive to the Chevrolet Vega, and plans to adapt it for other GM models were eventually shelved.
The Decline and Legacy of the Vert-A-Pac System
The Vert-A-Pac remained in use until 1977, when the Chevrolet Vega was discontinued. After that, most of the Vert-A-Pac railcars were converted back into traditional tri-level autoracks.
However, the legacy of the system lives on. It set a precedent for how logistics could influence vehicle design, manufacturing efficiency, and transportation strategy. While no other model would be shipped vertically again on a wide scale, the principles of maximizing shipping density and customizing logistics to product design are still highly relevant.
Today, the phrase “The Chevrolet Vega being loaded vertically” is more than a historical curiosity it is a testament to an era when innovation extended beyond the assembly line and into every aspect of a vehicle’s lifecycle.
Vertical Thinking in a Horizontal World
The story of the Chevrolet Vega and its vertical journey is an iconic chapter in automotive history. It exemplifies how manufacturers can benefit from looking beyond traditional methods and embracing radical solutions.
Although the Vega itself has been a subject of mixed reviews in terms of reliability and performance, the logistics approach behind its distribution remains a masterclass in engineering adaptation. It challenged conventions, inspired future innovations, and proved that thinking vertically in every sense can yield game changing results.